Osmacom Sandblasting & Painting procedure
Osmacom Sadat Plants
Sandblasting & Painting
Owing to our enriched industrial experience, we are devoted towards offering an excellent quality Sandblasting & Painting Services. The offered services are performed by our adept professionals using optimum grade machines and high-end technology.
What is Sandblasting of steel structure?
Sandblasting is a proven pre-finishing technique that’s been around for over a hundred years. The main use of sandblasting is removing and decontamination rust, loose mill scale, dirt, oil or grease and other foreign substances of bridges built up sections or any type of steel structure or PEB members. Osmacom Workers give Special attention to cleaning of corners and re-entrant angles. sandblasting is still the most common and preferred abrasive treatment method for final finishes.
What is Paint and How is structural steel paint done?
Paint is the most commonly used material to protect steel. The protective paint systems usually consist of primer, undercoat(s) and finish coats. Each coating ‘layer’ in any protective system has a specific function, and the different types are applied in a particular sequence of primer followed by intermediate / build coats in the shop, and finally the finish or top coat either in the shop or on site.
Osmacom always verify that paint materials are in compliance with the specification and this includes checking packaging and labeling; verifying the condition of paint in the container; and taking samples for testing. One of the most important inspection tasks we perform during a painting project is measuring the thickness of the paint coat to always make sure it’s the right thickness.
Osmacom also have undertaken various fireproofing steel structures projects- The very last of it was project: ” 10th of Ramadan Railway project -LRT “ – using Jotun Paints Steel Protection Systems and products such as:
Jotun Steelmaster 600WF – Jotun Steelmaster 1200WF.
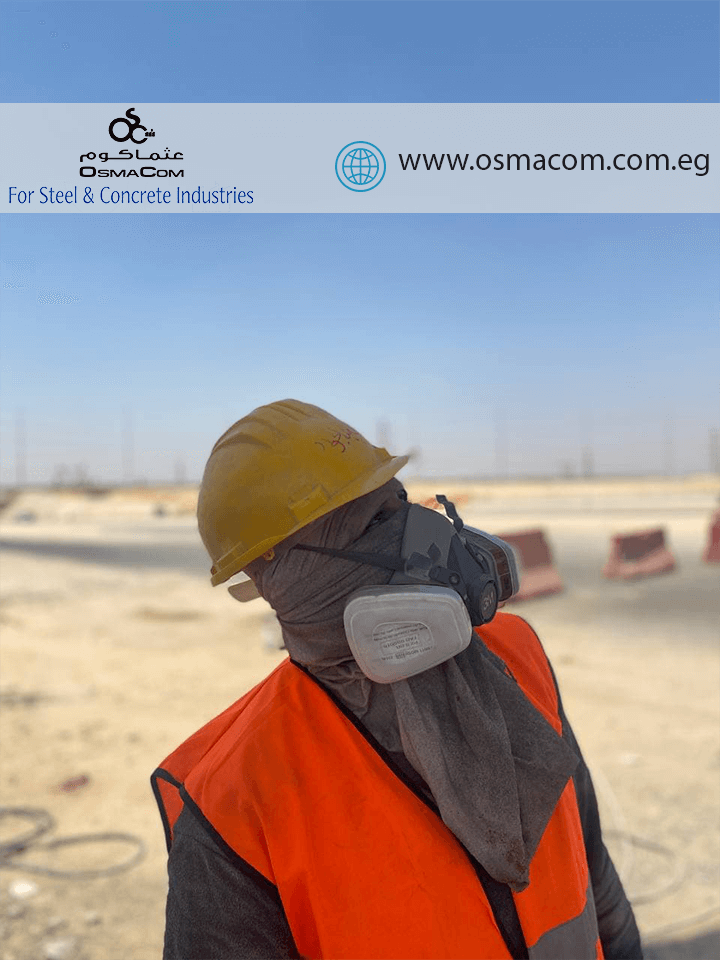
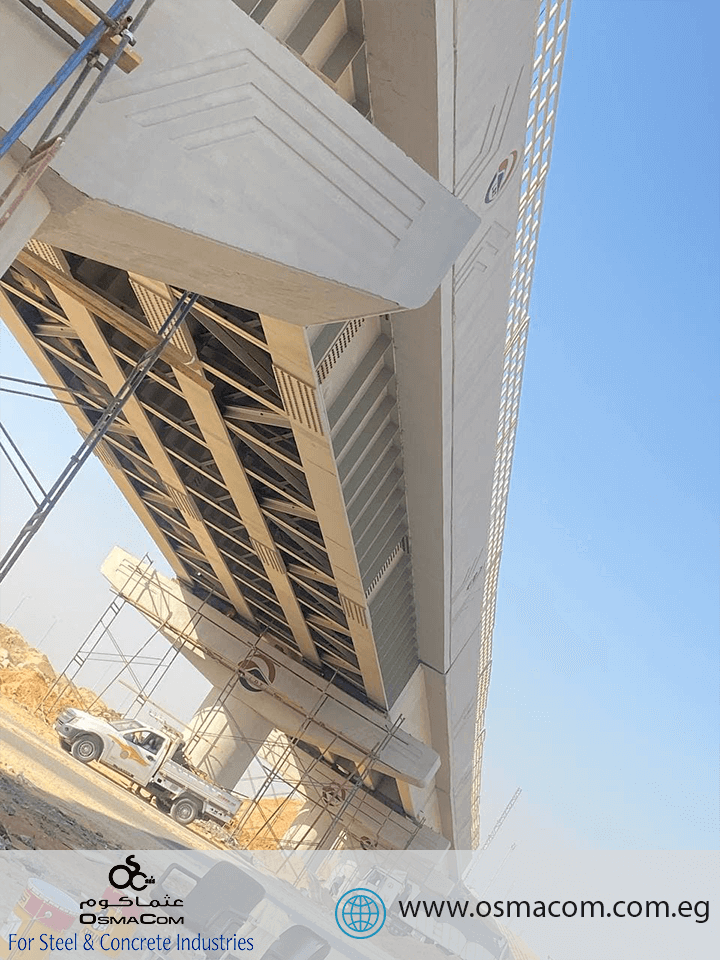
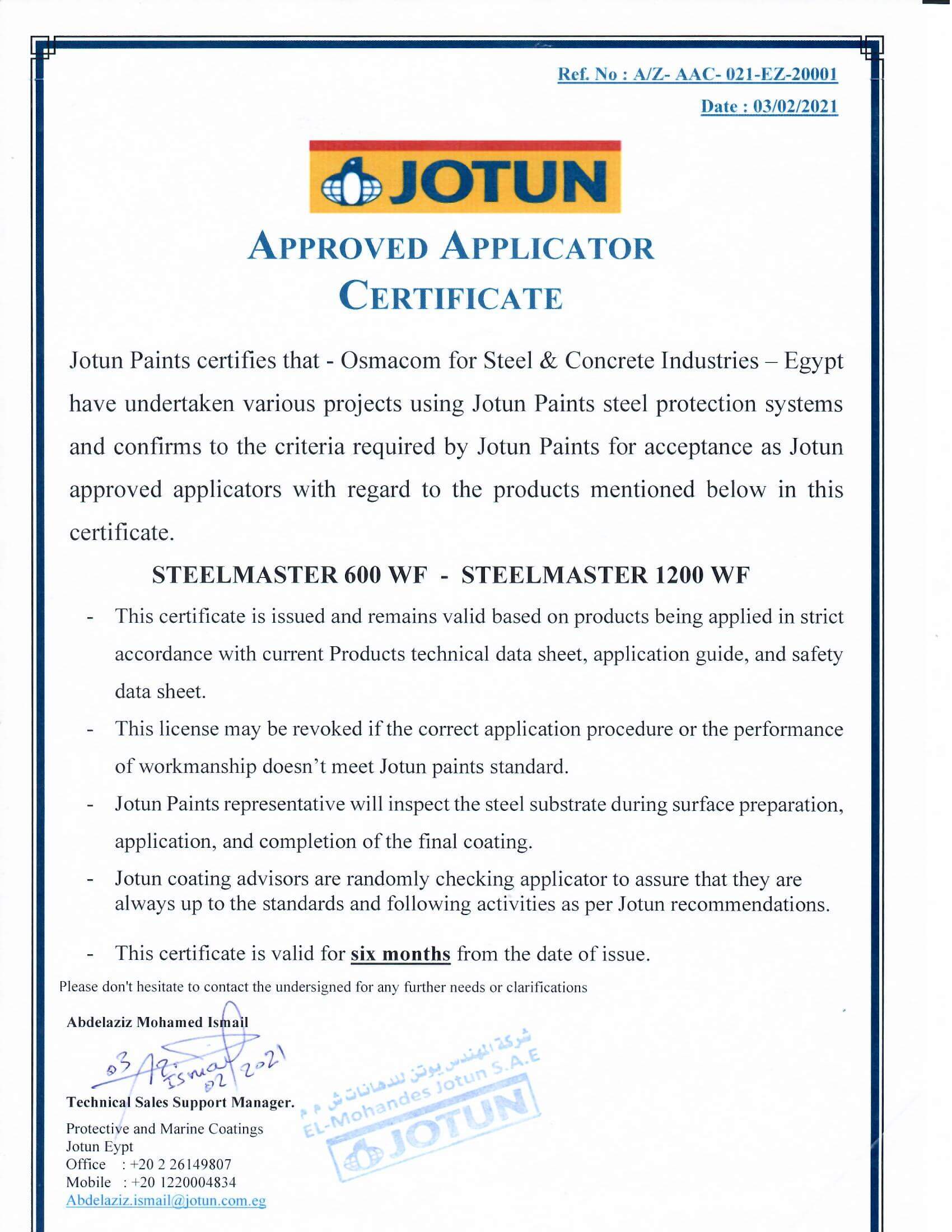
Osmacom Sadat Plants
Sandblasting & Painting Process Guide
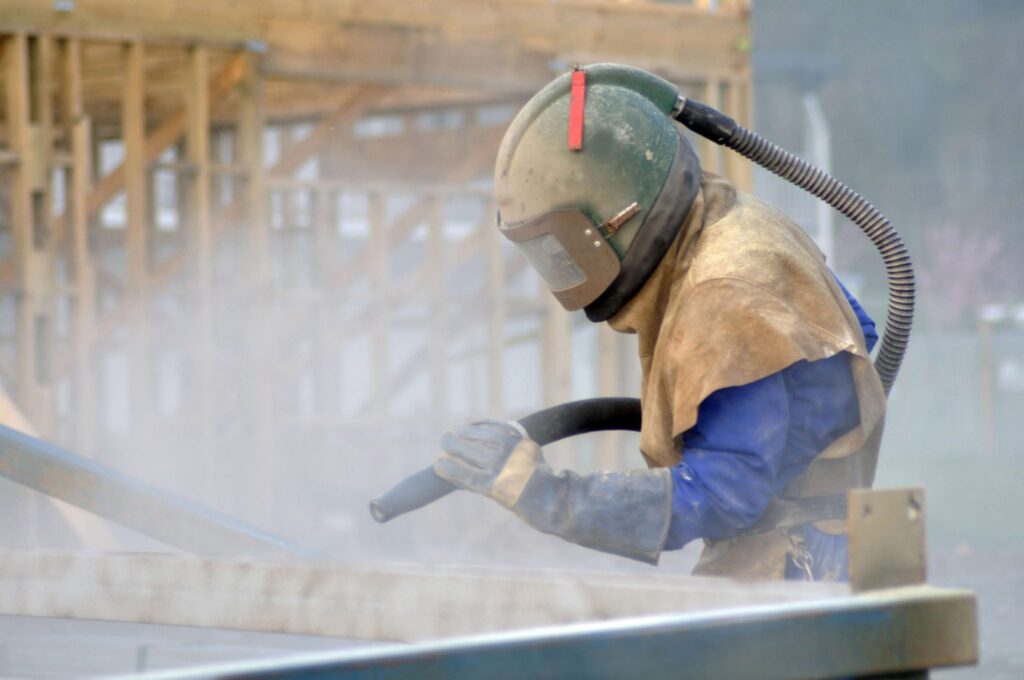
This Procedure covers the requirements for surface preparation and painting works for steel structures in OSC – Steel Division Workshop.
Equipment
■ Air Compressors equipped with built-in water and humidity separator & air receiver Tank
■ Sand Blasting Machine and accessories
■ Spray Machine and accessories
■ Blasting hose & Nozzle
■ Blasting mask, Aprons & Goggles
■ Paint Mixer
Instruments (Calibrated as per manufacturer recommendation)
■ Humidity Measurements Instrument
■ Dew point calculator
■ Temperature Instrument
■ Surface Profile Measurement Instruments
■ Wet Film Thickness (Manually)
■ Dry Film Thickness (Electromagnetic)
■ Pull off adhesion and cross cut adhesion tester
■ Pictorial reference for surface preparation and rust grade.
■ Clear self-adhesive tape for residual particulates check Materials & Consumables
■ Abrasive material for blast cleaning shall be carried out by using Sand, abrasive material shall meet the requirement of SSPC AB1.
■ Painting material batch test certificates must be submitted prior to execution the work.
■ All paints materials, and abrasive materials shall be approved by the Contractor and Company prior to their delivery and start the work
■ Paint system shall be demonstrated and approved by Contractor and Company, procedure qualification and Testing plan shall be approved by Contractor and Company
■ Material storage shall be as per the manufacturer’s recommendation. Shelf-life and pot life shall be monitored regularly.
■ All materials shall be kept dry, protected from weather and stored under cover, material temperature shall be kept between (5ºC – 32ºC).
■ Protective coating materials are to be stored according to manufacturer’s recommendations. Do not store near flame, heat or strong oxidants, Repair and
protective coating materials are to be handled according to their material safety data sheets.
■ Final Coat Color for steel structure is grey acc. to project specification, and final coat color for ladders and handrails as per client requirements.
Surface Preparation
■ Release for blasting and painting shall be obtained from the concerned department, drawing number, Item number shall be verified in accordance with the release note
(Form # OSC-QCF-05)
■ Visual inspection shall be carried out to ensure the cleanliness of abrasive blasting material is free from any contaminant that will prevent satisfactory surface preparation.
■ surface preparation shall not be carried out in unsuitable environmental conditions like:
– Steel and air temperature less than 5°C.
– Relative humidity more than 85%
– Airborne dust or sand
– Rain, fog, mist or when there is free moisture on the prepared surface
– Steel temperature less than 3°C above dew point of surrounding air.
– Where there is a likelihood that weather conditions will change within 2 hours that the above conditions apply
– Outside day light will be considered
■ Visual inspection shall be carried out as per SSPC VIS-1 prior to blasting to ensure the material is free from mechanical damage, weld spatter, sharp edges,
burrs, and also to assess the degree of contamination like dust, grease, oil, and Moisture etc.
■ Any weld spatter, sharp edges and burrs observed (if any) shall be removed by grinding, wire brushing, filling or chiseling.
■ Contaminations like dust, dirt, or moisture shall be removed with clean dry compressed air. If the extend of dirt is more, water washing and sponge
scribbling shall be carried to remove it. Grease, oil, etc. shall be removed by means of solvent cleaning or high pressure water jetting; solvent cleaning shall
be according to SSPC SP-1.
■ All sharp edges shall be rounded off by filling or grinding. No grit or foreign matter shall be left embedded in the blasted surface.
Air compressors shall deliver clean, and dry, supplied air temperature shall not exceed 110 °C. Accumulated water droplets shall be drained from the separators or filters
periodically. Periodic checking shall be carried out to ensure that the air delivered from a compressor is free from oil and moisture by blotting paper test if required; testing of
compressed air shall be according to ASTM D4285.
■Surface preparation (dry abrasive blasting) shall be carried out in general accordance with the following standards SSPC SP10, SSPC VIS-1 by using approved material with the
pressure at nozzle minimum 95 to 100 psi (665 to 700 kpa).
■ If the environmental conditions are favorable, blasting will be started at predestinated blasting yard. Proper surface preparation is achieved by maintaining an optimum speed
nozzle distance angle and overlap (minimum 25 mm into the adjacent area). The selection of aforementioned parameters and abrasive flow rate shall be decided by the abrasive
blasters.
■ If surface blast clean to Sa 2-1/2; Surface profile will be in the range from 25-50 microns; where the surface profile will be measured / checked by replica tape for recording. Post
blast cleaning, surface cleanliness shall be checked as per SSPC VIS-1 and to be recorded.
■ Blast surfaces shall be cleaned prior to primer by brush or blown to move as much residual particulate matter as possible and checked for residual particulate matter using clear self-adhesive tape as per ASTM D3359.
■ Area where abrasive blasting is practically not feasible shall receive a power tool cleaning to ST3 Standard after approval by the contractor QC Inspector.
■ Abrasive blasting will not be done in open areas close to painting operations or coated surfaces not yet dry as the blasting area shall be differs / separated than the painting area
one in order to prevent dust and abrasive contamination.
■ Primer coats shall be applied immediately after completion of surface preparation, where any flash rusting occurred due to delays between blasting and painting shall be given a
sweep blasting before painting.
■ Area prepared by power tool and/or hand tool cleaning shall be primed within maximum 4 hours and never left unprimed overnight.
■ Surface after blasting shall be checked as per SSPC VIS-1; the surface shall be free from visible oil, grease and dirt and from mill scale, rust and foreign matter prior to paint
application.
Painting
■ Application procedures shall conform to the recommendations of the protective coating manufacturer and Client Specification, including material handling, mixing, and
environmental controls during application, safety, and manual or spray equipment.
■ The method of application shall be governed by paint manufacturer’s recommendation for particular paint being applied.
■Mixing ratio, thinner percentage, pot life and over coating interval shall strictly be adhered as per the paint manufacturer’s product recommendation.
■ Spillage of all materials will be cleaned immediately to prevent contamination.
■ All paint application will be carried out by suitable trained / experienced operators.
■ Paint Manufacturer recommendations on temperature limitations for paint application shall be complied with.
■ All works will be carried out in dry and atmospherically correct conditions.
■ The working area will be kept clean at all times.
■ No painting operation shall be done in the following weather conditions at the working area:
– High Wind Speed.
– Steel and air temperature less than 5°C.
– Relative humidity more than 85%
– Airborne dust or sand
– Rain, fog, mist or when there is free moisture on the prepared surface
– Steel temperature less than 3°C above dew point of surrounding air.
– Metal Temperature greater than 49°C
– Where there is a likelihood that weather conditions will change within 2 hours that the
above conditions apply.
■ Application equipment approved by the coating manufacturer shall be used to apply each coat of the protective coating.
■ Prior to painting a thorough cleaning of the blasted surface shall be carried out with clean dry compressed air to remove all dust and embedded abrasive particles.
■ Painting shall be carefully done in such way as to give coating free from lifting, poor adhesive discoloration & finished to uniform paint film thickness.
■ Painting shall be carried out by airless spray to achieve the specific film thickness. The spray width and pressure adjustment shall be carried out to achieve the desired spray
pattern. The Spray gun shall be according TDS and item shape and should be held at right angles to work surface.
■ The spray gun shall be triggered before and after each passes to avoid runs and sage.
■ During each stages of coating the required WFT shall be measured .
■ High pressure washing if required and abrading will be considered between coats.
■Mixing of paint (Homogenizing) shall be as follows / as recommended by manufacturer;
a. The paint Drum shall be opened and the bulk of liquid portion shall be poured into a clean drum of similar size with an open top.
b. The residual stiff or lumpy settled material shall then be broken up stirring with a strong wooden paddle. After that the liquid portion shall be poured into and stirred
with mechanical power driven stirrer to get a smooth and uniform paste. Even after stirring , the residue cannot become smooth & uniform then that paint shall be discarded
c. When the residual paint in the original container is dissolved & mixed uniformly, it shall be boxed by pouring repeatedly between the liquid portion skimmed earlier and
the residual past
d. Thinner material in the required proportion as specified in material data sheet for the particular type of paint shall be used for homogenizing the paint material
■ Mixing of Two component packs:
a. Paints supplied as two components in separate containers shall be mixed as together immediately before use and shall be applied within the time limits specified
by the manufacturer.
b. The method of preparing those of types of paints before use shall be carried out based on the type of paints.
■ Surfaces to be paint shall be thoroughly cleaned and shall be maintained free from moisture prior and to during paint application.
■ Over-coating items shall be in strict accordance with the paint manufacturer’s instructions and should be carried out as closely as practical to minimum recommended time.
■ If necessary, subsequent top coating or additional coats of the protective coating should occur as soon as the basecoat becomes tack free, ideally within 12 hours but no later
than the recoat window for the specified products. Additional surface preparation procedures will be required if this recoat window is exceeded.
■ Painting shall be carefully done in such way as to give coating free from lifting, poor adhesion and finished to uniform paint film thickness.
■ Thinners shall only be used as recommended by the paint manufacturer.
■ When the surface to be painted is wet, but unavoidably requires to be coated, painting shall be done after full wiping and complete drying of surface.
■ Subsequent over coating of paint shall be made after checking the dryness and degree of cure of pervious paint films. Any defects, on coated portions, deposits, etc., shall
also be checked and completely repaired prior to over coating.
■ No thinner is allowed to be adding to mixed paint unless written instruction from paint supplier.
■ Primer coat application by brush is only allowed for strip coat and small areas as per Primer Data sheet.
Repair & Touch up :
■ Damaged areas or loose, cracked, brittle or non-adherent paint shall, however, be removed and re-painted after surface preparation to the original standard with the
same number of coats and brands of paints as originally applied.
■ Defects (IF any) observed shall be repaired to achieve the property of original coating.
Testing , Inspection and Quality Records
■ Testing and Inspection shall be performed according to approved Inspection and Test Plan for surface preparation and painting works, this shall be as a minimum include the
inspection and test activities that are identified in clause 10 of the project specification for painting.
■ All measuring equipment shall be calibrated and have valid calibration certificates.
■ After the film is sufficiently dry or cured, DFT to be checked with approved model magnetic or electromagnetic or eddy current meter. Prior to measuring DFT meter shall
be calibrated using standard foils.
■ The selection of materials, mixing, application and achieved DFT will be overseen and monitored properly by the foreman, and QC inspectors, referring to respective technical
data sheet for details on mixing and application.
■ The visual inspection shall be carried out after each coat to ensure the shade, degree of gloss, evenness, freedom from tackiness after drying/ curing .cracks, holidays , runs,
sage, wrinkles, patches, deep brush marks etc.
■ 45 degree X cut as per ASTM D 3359 shall be carried out to ensure the coating system meets the performance requirements.
■ All coats shall be applied free from runs, sagging, holidays or curtaining … etc., and minimum dry film thickness shall be strictly adhered for each coat applied.
■ All touch- up/repair procedures, for areas that do not meet the specified thickness, shall follow the protective coating manufacturer’s recommendations and SSPC PA2.
■ Quality documents (Form # OSC-QCF-017) shall be prepared and submitted to the contractor and Company for approval.
Safety
■ All blasting / painting equipment are calibrated and in good working condition
■ All working crew shall wear PPE for the tasks as per section 5.2 Blasting mask, Aprons and Goggles.
■ All potential sources of ignitions shall be strictly controlled and sparks, hot surfaces, flames shall be as per manufacturer’s recommendations.
■ Storage of chemical shall be as per manufacturer’s recommendation.
■ OSM shall ensure that all activities involved in the selection, application, inspection and testing of protective coating systems are managed to ensure personnel safety, minimal
environmental impact and safe.
■ All waste disposal material, including but not limited to spent abrasives, coatings,
thinners, solvents and cleaners shall be handled in a safe and legal manner and shall
comply with all applicable regulations and laws.
■ Implementation of safety measures for protecting workers in accordance with all local and national regulations including provision of appropriate personal protective
equipment and training in its use, regular safety briefings/tool-box talks etc.
■ Provision of appropriate RPE and PPE.
■ Hearing protection requirements for blasters and those working nearby, warning signs at entrance for particular extra PPE requirements.
■The blasting PPE, specifically the Blasting mask like a face shield or a helmet type with air supply shall be used.
■ RPE and any other specific PPE requirements for non- blasting personnel in the area,
i.e. cleaning up after blasting, Fire watcher, Alarm watcher, supervisors and safety officers and the occasional worker walking by.
■ Apron and rubber gloves for painters..
■ Provision of appropriate fire-fighting equipment.
■ Provision of appropriate first aid facilities. Collection and removal of spent sand, empty solvent and paint cans shall be carried out on daily basis or if required and disposed in
approved dumping sites.
■ An appropriate Paint Storage area shall be provided.
■ An appropriate Paint mixing area, methods, preparation and precautions of paint mixing shall be provided.
■ Appropriate disposal methods and regime shall be provided i.e. empty paint cans, drop sheets, spill mitigation, unserviceable paint equipment, and used blast particles disposal.
■ Means of paint, thinners, or other chemical spill mitigation shall be provided.
■ Blasting Areas separated/segregated from Painting areas, (by time or location)
■ Blasting /Painting Areas separated/segregated from other work areas.
■ Air compressors, Air hose Safety Whips, Blasting nozzles and hose earths.