Welding Check ( NDT)
Osmacom Quality Control
What is NDT? and What methods are used to test welding?
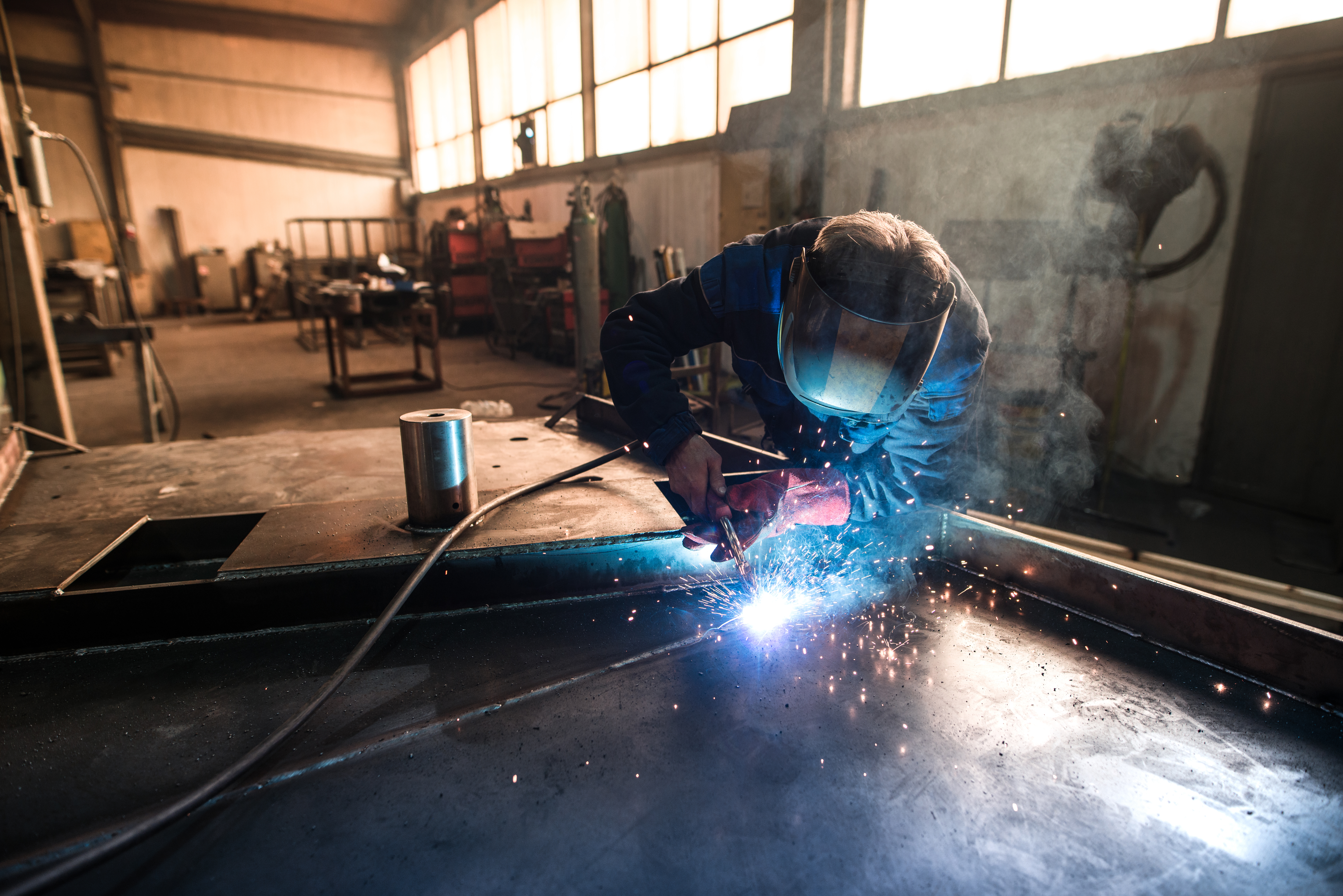
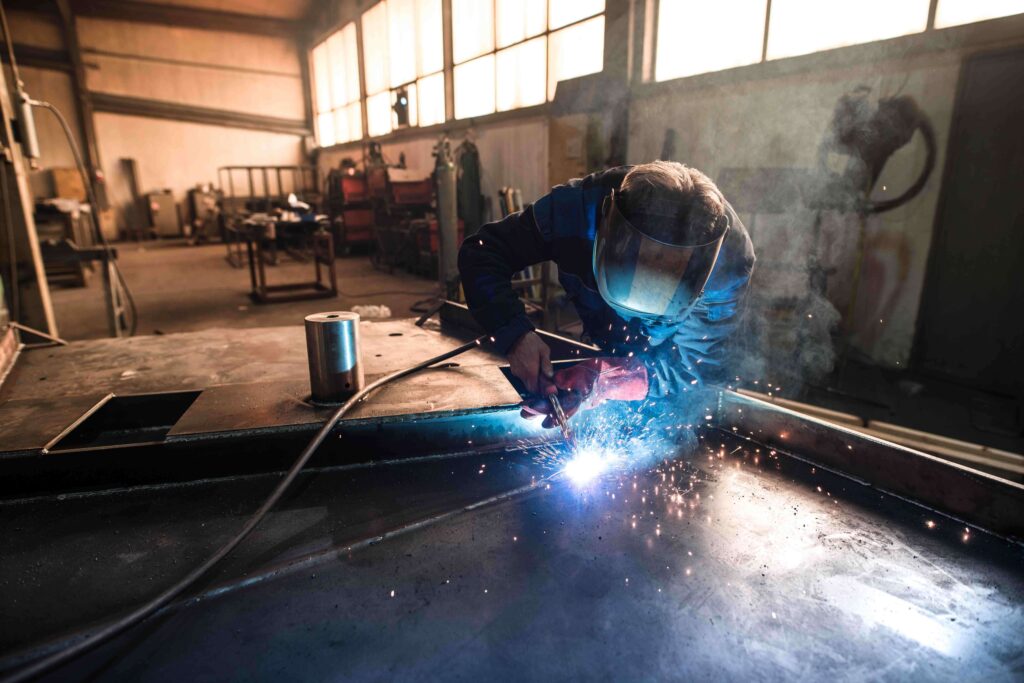
Non-destructive testing (NDT) is a testing and analysis technique used by Osmacom Quality Control Department to evaluate the properties of steel structures and Pre Fabricated members for characteristic differences or welding defects and discontinuities without causing damage to the original part.
VISUAL INSPECTION PROCEDURE
Visual inspection is one of the most important methods of inspection and is probably the most widely used for many types of welds where the quality can be verified with visual inspection alone.
Purpose of the test:
The purpose of this procedure is to ensure that all visual inspections are performed in a controlled manner and are acceptable to the project specification, QCP’s and controlling codes.
References
• OSMACOM SPEC
- EN ISO – 13920
• AWS D1.1
Procedures of the test:
1 – The visual inspection shall be performed both prior to, during and post welding, engineering & construction activities, to ensure full compliance with the relevant codes, drawings and specifications.
2 – All equipment used as either as part of, or to assist visual inspections shall where applicable, be fully calibrated and have a valid calibration certificate.
3 – The QC inspector shall be suitably qualified to a recognized international standard for the inspection and shall check the item or component against the appropriate QCP, drawing, specification and / or code to ensure full compliance.
4 – The surface condition for visual inspections shall be clean and must be such that it will not interfere with the interpretation or results.
5 – QC personal who are required to perform visual inspection shall possess good eye sight and be able to pass a standard J-1 Jaeger test or be able to distinguish a flaw of 0.79 mm in size. If the QC inspector is required to wear visual aids such as glasses, then these must be worn during the inspection.
6 – In the event that the surface cleanliness is insufficient, then the surface shall be cleaned by a suitable means i.e. scraping, wire brushing, etc. until the desired cleanliness is achieved. The means of cleaning shall not be detrimental to the item under inspection.
7 – Only direct viewing means shall be used for visual inspection and the minimum illumination shall be 10 lux at one meter. Where lighting is insufficient the inspector shall use a suitable method of artificial illumination such as a torch.
8 – During the inspection, the inspector shall check as a minimum: –
- Surface preparation
- Item fit up
- Surface defects, Material type & grade
- Misalignment
- Surface finish (where applicable)
- All relevant dimensions which have an effect on quality Cleanliness
- Compliance to all specification, code, procedural or controlling tolerances / parameters.
- That items which are to be covered are fully acceptable and documented prior to progression and cover up.
9 – All weld seams shall be suitable offset and any surface defects shall be removed by grinding and the check by NDE to both to ensure their removal and that there is sufficient parent material left in place.
10 – During welding operations, the following shall also be checked visually: –
– WPS
– Welding process including current, voltage & polarity
– Direction of welding
– Travel speed
– Heat input
– Welding consumable used
– Welding technique
– Inter pass cleaning
– Welder Qualifications
11 – Upon successful completion and acceptance of the visual inspection, the QC inspector shall record the results on the relevant QCP and complete all necessary QC inspection & record forms and the item shall be identified & recorded as inspected and accepted.
12 – The rejected item shall be re-worked as required until it conforms to the required specification / tolerances, at which time it shall be re-inspected.
13 – For items which are subject to final visual inspection upon completion, in the event that these are non con forming, then these shall be reported on a NCR
14 – Upon completion of the visual inspection all associated records; these shall be filed in the KPC QC file with a copy supplied to KPC Co.
LIQUID PENETRATE TEST
The Liquid Penetrate examination method is an effective means for detecting discontinuities, which are open to the surface of nonporous metals & other materials (ferrous& nonferrous metals). Cracks, seams, laps, porosity & laminations are defects typically detectable by this method of testing.
Purpose of the test:
The purpose of this procedure is to ensure that all P.T. inspections are Performed in a controlled manner and are acceptable to the project fabrication Specification, QC P’s and controlling codes.
References
-ASME V Article 6
-AWS D1.1
-OSC specification
Procedures of the test:
– Application
Procedure should meet the requirement of ASME V article 6, and material should meet the requirement of ASTM E165
– Personnel Qualifications
Personnel performing PT inspections and interpreting the results shall be qualified in accordance with the requirements of ASME V and SNT-TC-1A Level II or III
– Surface Preparation
1-In General Satisfactory Results may be obtained when the surface of the part is in the as-welded, as rolled, as-cast, or as-forged condition. Surface Preparation by grinding, machining or other methods may be necessary where surface irregularities could mask indications of unacceptable discontinuities
2- The surface must be clean from all dirt, grease, scale, welding flux, weld spatter, Paint, oil & other extraneous matter that could obscure surface opening. All adjacent test area within 50 mm at least shall be dry.
– Material
1- NEOPEN (JAP) penetrate 2- NEOPEN (JAC) cleaner &remover 3- NEOPEN (JAD) developer | Or | 1- ELY Chechmor 222 penetrat 2 – ELY S – 72 cleaner & remover 3- ELY LD3 developer |
– Type
Visible-Solvent removable dye Penetrate shall be used
– Inspection Procedure
- Application of penetrates: –
Penetrate shall be used by spraying on test area (weld area) far away by 12 inches inclined by 45° with maximum temperature 30°c, wet surface shall be allowed from (3 –5) minutes before removing the penetrate. (Dwell time) or as according to instruction of the manufacture.
- Removal of excess penetrates: –
By wiping the surface with a clean dry cloth to remove the excess Penetrate (3– 5) min.
- Application of developer: –
– Spraying area to be inspected with a thin layer coat of developer.
– Developing time from (5 to 10) minutes before the interpretation.
– Illumination
All (PT) testing shall be performed in adequate lighting, so to aid Interpretation of the results.
- Upon successful completion and acceptance of the PT inspection, the QC inspector shall complete all necessary QC inspection & record Forms The item shall be identified & recorded as inspected and accepted.
- In the event that the PT inspection is unacceptable, the item shall be Rejected and identified as such. The QC inspector shall record the results of the rejection on the relevant QC PT inspection QC form and amend all Other QC records to reflect this rejection. The rejected item shall be re-worked as required until it conforms to the Required specification / tolerances, at which time it shall be reinserted.
MAGNETIC PARTICLE TEST
MPI shall be considered as a means of detecting surface & subsurface defects only. Therefore, this procedure may be used to disclose surface breaking discontinuities, but may be applied to all shapes and configurations of Ferro-magnetic materials
Purpose
The purpose of this procedure is to ensure that all MPI inspections are performed in a controlled manner and are acceptable to the project fabrication specification, QC Persons and controlling codes.
References
– ASME V Article 7
– Non Destructive Testing
– AWS D 1.1
Procedures of the test:
- Application
Examination will be done according to ASME V article “7”
- Personnel Qualifications
Personnel performing MPI inspections and interpreting the results shall be qualified in accordance with the requirements of ASME V and SNT-TC-1A Level II OR III
- Surface Preparation
Prior to the application of the white contrast paint, the substrate shall be thoroughly cleaned by means of wire brushing or grinding . The surface shall be free of all loose scale, weld spatter, slag, oil, grease, dirt, or other undesirable items which may interfere with interpretation of the test results, shall be completely removed.
- Materials
1- ELY(Paint 712)White Contrast Code No 2614
2- ELY Magnetic Particle Ink Code No 2348
- MPI Black Inks
The Ferro-magnetic particles must fulfill requirements of being non toxic and be of a high permeability.
The magnetic particle ink shall be kept free from all deleterious material, which might interfere with its proper function.
Wet Black inks shall be used and will normally be supplied in pre-sealed aerosol containers
- Background Contrast Paint
The white contrast paint shall be used as an aid to interpretation. Care shall be taken when applying the contrast paint that it is not applied too thickly, as this could mask defects and hinder interpretation.
The white contrast paint shall be supplied in pre-sealed aerosol containers (NEOPAINT).
- Equipment
The equipment to be used for MPI shall be as follows :-
-Y6 Yoke with variable poles (AC current 220v) AC power supply with the capacity to lift a weight of 4.5 kg with poles at the maximum spacing of 100 mm.
-White back ground contrast paint
-Magnetic particle black ink (wet)
-Hand wire brush
- Inspection Procedure
– After attaining the required cleanliness, the white background paint shall be agitated and applied as thinly as is practically possible in order that it will not mask small defects or reduce sensitivity.
-A suitable power supply shall be supplied when using Y6 electric yoke type magnets. The magnet shall have its poles spacing set at 100 mm (maximum), and be positioned at an angle of 45 across the weld.
– The wet black ink shall be vigorously agitated and applied to the surface under test in a fine spraying action with the magnet energized.
Any indications shall be observed and interpreted.
The magnet shall then be moved to 90to that of position A-A, to B-B as shown in Fig 1 above.
The procedure as given in 5.7.1 shall be repeated.
The steps as given in 5.7.2 & 5.7.3 shall be repeated until the entire length of the weld has been inspected.
– All indications of defects shall be observed and reported.
– Upon completion of the test, the surface which has been tested shall be cleaned of all MPI residue by either wire brushing or grinding.
- Illumination
All MPI testing shall be performed in adequate lighting, so to aid interpretation of the results.
- Upon successful completion and acceptance of the MPI inspection, the QC inspector shall complete all necessary QC inspection & record forms.
The item shall be identified & recorded as inspected and accepted.
- In the event that the MPI inspection is unacceptable, the item shall be rejected and identified as such. The QC inspector shall record the results of the rejection on the relevant QC MPI inspection form and amend all other QC records to reflect this rejection.
The rejected item shall be re-worked as required until it conforms to the required specification / tolerances, at which time it shall be re-inspected.
RADIOGRAPHIC TEST
- Scope
The procedure shall be applied to all radiographic inspection carried out during execution specification of the project material API 5L X60 different size & thickness
- Purpose
The purpose of this procedure is to ensure that the produced radiographic image is of an acceptable quality and that all radiographic inspection are performed in a safe and controlled manner and conform to project specification and controlling codes.
- References
- ASME V, article 2
- SNT-TC-1A
- API 1104
- ASTM E 1390
- ASTM E 1079
- ASTM E 94
- ASTM E 797
- Definitions
Examiner
Only personnel who are fully trained and qualified, with adequate experience shall be permitted to undertake radiographic inspection or handle radioactive sources.
- Procedure
- General: Gamma ray isotope with focal spot size as follows : ( for Little Welds And Tie – In )
Isotope : Type – IR 192
Activity : Up to 60 curie
Effective source size : ø 2.7 mm or 2 X 3 mm
Half life period : 74 days
X-RAY Machine ( for Long Strings have Many Welds)
Type of equipment : Crawler 350 kv
Isotope : Type : Cs 137 (for Control Only)
Machine Intensity : UP to 350 KV
Focal spot: 1.5×5 mm
- Pentameters :-
Wire pentameters type shall be used according to Din (10-16) .
- Intensifying Screens :-
Lead PB intensifying screens shall be used “lead thickness 0.1 mm”
- RT Technique:-
Radiographic technique shall be DWSI & SWSI.
Radiation Type Gamma
Agfa D7
Kodak AA400
Equipment
- Isotope radiograph source (IR 192)
- RT device of isotope radiograph
- Lead screen film
- Lead alphabetic letters, numbers and number tape
- Survey-meter
- Cable for RT device (behind & forward)
- Densitometr
- Dosemeter
- Badgefilm
Radiograph Identification
All radiograph shall contain all data for every film of the weld joint, the radiographic image identification shall include the following information:-
- Project name
- Company name
- Weld no.
- Date of radiograph
- Size of weld joint (diameter & thickness)
- Item no.
- Welder no.
Examination
- Pentameters:
- IQI shall be placed on right angle with the weld being examined close to joint Identification.
- The pentameter shall be present at area of essentially uniform radiographic density.
- Penetrometers should be place at the center for each radiograph.
- 1.4. Where one or more exposure holders/cassettes are used for an exposure, a pentameter image shall appear on each radiograph, except where the source is placed on the axis of the object and the complete circumference is radiographed with a single exposure, in this case at least three equally spaced film side pentameters shall be used.
- Back Scatter Radiation:
As a check on the back scattered radiation, a lead symbol “B” shall be attached to the back of each film holder. If the image of the “B” appears on a darker background of the radiograph, the radiograph shall be unacceptable; a dark image of the “B” on a lighter background is accepted.
- Geometric un-sharpness:
Geometric un-sharpness of the radiograph shall be determined in accordance with the formula as follows:-
Ug = F * (T/D)
Ug = Geometric un-sharpness
F = Focal spot size
T = source object distance.
D = Distance from source of radiation to weld
** Final acceptance of radiographs shall be based on the ability to see the prescribed pentameter
image and the specified wire depends on radio graphed weld thickness.
** Geometric un-sharpness of the radiograph shall not exceed the following :-
Item Material thickness (inch) Maximum Ug
1 Under 2″ 0.020
2 2″ through 3″ 0.030
3 Over 3″ through 4″ 0.040
4 Over 4″ 0.070
The examined part could be pipe, sheet, plate or steel structure.
Radiographic density :-
- The transmitted film density of the radiographic image of the body that adjacent to the designated wire of a wire pentameter and the area of interest shall be 1.8 min and 4.0 max for Radiography by gamma ray & 2.0 min and 4 max for X ray.
- Density variation: Generally the density of the radiograph anywhere through the area of interest varies by more than minus 15% or plus 30% from the density adjacent to the designated of a wire pentameter within a minimum /maximum allowable density range specified above.
- Measuring radiographic density by using the densitometer.
- Sensitivity: The accuracy of radiographic image is called sensitivity and the value of it, is Max 2.0%.
Type of Technique
General: The types of technique are the method of applicable way to make a radiographic image according to the size, geometric shape of examined objects, the position of object and facility to make radiographic image.
- Double wall single image and Single wall single image technique shall be used for radiographic inspection when it is practical.
- Double wall viewing: Applicable techniques for pipe diameter 2″ and less, the radiation passes through two walls and the weld material in both walls are viewed; in this case, the source will be placed away from the centerline of the weld.
Processing of the Film
The instructions relating to the film chemicals concerned should be complied with the processing the film. Film processing shall take place in a darkroom and shall also be air-conditioned to prevent overheating of the process chemicals and be totally lightproof.
The safe lights used during processing shall conform to the requirements of ANSI PH2.22.
- Manual Processing Steps :-
- Remove the shielding lead screen which cover the film.
- The film shall be put in developer path (tank) for 3-5 minutes.
- Stop path by getting out the film from the developer path and put it in fresh water.
- The film shall be put in fixer path after cleaning for 5-10 minutes.
- Washing the film by water after getting the film out the fixer path.
- Washing the film in clean water for minimum of 4 minutes to ensure remove of resultant chemicals and thus ensuring the correct archival life without detrimental effect .
- Drying the film by forced hot air (dryer) or by heating the film.
- Interpretation
The interpreter must be qualified and certified level II according to ASNT. The interpretation shall be done with respect to the specification of project and acceptance criteria of code.
- Documentation
After making interpretation and evaluation, the result shall be written in the RT report and submitted to client for approval.
- Safety Requirements
- PURPOSE
The purpose of this procedure is to provide instructions for controlling the use of ionizing radiation sources for radiographic examination. The full requirements of the Site Safety, Health & Environment Plan shall also be complied with when performing non-destructive testing using radiation sources.
- SCOPE
This procedure covers all non-destructive testing activities performed including X-rays and gamma rays from ionizing sources
- REFERENCES
“Radiation Safety For Site Radiography” – Klower Press
“The Ionizing Radiation Regulations 1985” – HMSO (SI 1985 No.1333)
“The Protection Of Persons Against Ionizing Radiation Arising From Any Work Activity” U.K.
Health & Safety Executive.
Radiography Operations
General.
- Petrojet will be required to provide Material Data Sheets for each ionizing radiation source. It shall be made available to the Client with a copy provided to the medical centre.
- Data sheets contain, as a minimum, the following information:
- Generic or Trade name and supplier
Chemical name or element name.
- Size and physical properties.
- Current strength and half life of radiation source.
- Storage, packaging and labeling
Work Methods:
- Petrojet will barrier off the area and check to ensure that all personnel have been vacated from inside the barriers, including above and below.
- At the discretion of the Site HSE Supervisor, a wind-out test may be required to ensure that barriers have been erected at a safe distance.
- On completion of the work the Contractor will return the source to its storage area and remove-all barriers and equipment.
- No eating or drinking is allowed within the controlled area.
Personnel Qualify
- Only suitably trained and experienced personnel will be used in radiography work on the pipeline.
- Training records and certificates for all nominated personnel must be available .
- Dose rate records for personnel should be carried forward from past employers.
- All persons in the radiography team must be familiar with site and radiography emergency response procedures.
- All radiographer trained and qualify
- The RT Personal Should Be Qualified And Certified According To ANST Under Practice SNT-TC-1A
- Level II Or III
Vehicles and Equipment
- Radiation monitoring equipment shall be fully calibrated and certified correct prior to and during use.
- Certificates containing source details must be available. These details include the decay table, serial number, type and half life of all radioactive sources to be used on pipeline.
- Advance notice of source transportation, with source container serial numbers and certificates, must be submitted before any movement of sources.
- Monitoring equipment must be calibrated, tested and certified.
- Sufficient barriers and signs are to be available before start of work.
- Defects in equipment must be immediately reported to radiography supervisor for remedial action.
- The work team must have emergency handling equipment.
Medical Arrangements
- All personnel engaged in radiography will be subject to 6-monthly medical examination. Examination results will be available at Petrojet Northern Branch Office, and copies will be held at site
- Film badges are to be worn by all radiography personnel.
- Film badges are to be checked monthly and the results recorded.
- Personal dosimeters are to be used by crewmembers operation.
- Any accidental overexposure to radiation must be immediately reported and medical assistance obtained.
Storage of Isotopes
- Sources will be kept in the approved storage facility at Petrojet yard when not in use.
- Each time a source is moved in or out of the storage facility the source register will be marked accordingly.
ULTRASONIC TEST
- Scope
The scope of this procedure shall apply to ultrasonic carried out during the execution of the project; this procedure specifies the equipment, materials and qualifications which are required for ultrasonic of welds and materials.
- Purpose
The purpose of this procedure is to ensure that all ultrasonic inspections are
performed in a controlled manner and are acceptable to the project fabrication specification, and controlling codes.
- References
– ASME V Non Destructive Testing
AWS D 1.1 Non Destructive Testing
- Procedure
4.1 General
Ultrasonic inspection shall be considered as an alternative means of detecting
internal defects &lamination check when it is impractical to use radiography.
4.2 Personnel Qualifications
Personnel performing ultrasonic inspections and interpreting the results shall be qualified in accordance with the requirements of ASME V and SNT-TC-1A, to ASNT II or equivalent.& level I for lamination check
4.3 Couplant
The couplant used to aid the transference of the ultra sound into the material under test shall be non toxic and shall not cause any harm to the test component.
4.4 Transfer correction Factor
The maximum correction factor permitted for the transfer of ultrasound from the probe into the work piece shall be 6dB.
4.5 Distance Amplitude Correction Curve (DAC)
A Distance Amplitude Correction curve (DAC), shall be produced using the required reference block as stated in API 1104 .
Ultrasonic Inspection, any indication which reaches 90% DAC height, shall be
investigated and assessed. Any indication, which equals or exceeds DAC height
shall be rejected.
4.6 Equipment
The equipment to be used for Ultrasonic inspection shall be as follows:
* Ultrasonic Flaw detector e.g. USK7, Sonatest, etc. which displays ‘A’ scan information.
* A 0 compression wave probe.
* 45, 60 & 70 shear wave probes.
* Probe cable leads ( which shall be in good condition ).
* Paste couplant.
* V1 & V2 calibration blocks.
4.7 Ultra sonic Probes
All ultrasonic probes used shall have a probe frequency of between 1-5 MHz, with the probe index and emission point clearly marked.
The smallest defect detectable is approximately half the size of the probe wavelength, therefore frequency selection should be as high as practically possible for the material under test.
Probes shall be of such a design that the ‘dead’ zone is contained within the probe itself and where ever possible twin crystal probes shall be used to reduce any undesirable effects of the near zone.
4.8 Surface Condition
The surface area either side of the scanning test zone shall be wire brushed or ground to remove any weld spatter / irregularities etc., and to produce a smooth surface finish for scanning. The extent of this cleaning shall be marked by the ultrasonic inspector and shall extend for a 100 mm or the distance required by any probe for the full skip distance.
4.9 Calibration
Prior to commencing any ultrasonic inspection, the CRT linear time base of the ultrasonic flaw detector shall be fully calibrated for each probe used.
The V1 calibration block shall be used to check and mark the index / emission point and angle of the probe.
The V2 calibration block shall be used to calibrate the CRT linear time base for the ultrasound path distance through the steel.
Calibration should be checked regularly during inspection, but shall be checked as minimum every time the ultrasonic set is switched on, the batteries are changed, the probe is changed, or every 4 hours of continuous work.
4.10 Scanning Technique & Sensitivity Level
The sensitivity setting for weld scanning shall be the V1 block 1.5 mm hole, set to Full Screen Height, plus the 6dB transfer correction factor.
For compression probes, after calibration the probe shall be positioned onto the area of interest and the reading observed.
For shear wave probes, after calibration the probe shall be moved in a ‘zig zag’ motion perpendicular (90) to the along the weld under test.
The maximum speed of longitudinal travel along the weld (length ways) during test shall not exceed 50 mm per second.
4.11 Inspection Procedure
4.11.1 As a minimum requirement ultrasonic examination shall be conducted using a compression probe and one of three angled transducers, usually 45°, 60° and 70°, operating between 1 and 5 MHz . Ultrasonic examination shall be conducted from both sides of the joint and, if access permits, from both inside and outside surfaces.
4.11.2 The couplant shall be applied to the surface under test in sufficient quantities to eliminate the air gap, but not excessively, as large a build up of couplant on the probe may be the cause of spurious indications.
4.11.3 The plate / surface of the item under test shall be scanned using the 0 probe to check for any laminations in the material and to confirm the thickness of the material.
4.11.4 If no laminations are present, the weld scan shall then be performed as described in 4.10, using any of 45, 60 & 70 shear wave probes.
4.11.5 In the event that defect indications are located, then they shall be sized as stated in
of this procedure.
4.11.6 All defects that fall outside the relevant acceptance criteria shall be rejected and reported.
4.11.7 Upon completion of the ultrasonic inspection the work piece shall be cleaned and all couplant removed.
The cleaning operation shall take extreme care so as not to remove any indications of defects which have been marked.
4.12 Defect Sizing
The ultra sound beam shall be located over the defect and the signal maximized. The shall then be moved off the defect until the signal on the screen reduces to 50% of the maximized signal and the area marked on the work piece. This shall be repeated for all boundaries of the defect, i.e. length and width until a suitable image of the defect is established. The physical dimensions shall then be recorded directly from the work piece.
4.13 During production examination of welds, the PETROJET shall produce test reports outlining the technique employed and the defects discovered.
The report shall contain the following information as a minimum:-
- a) weld number
- b) welding procedure
- c) face width of unacceptable defects
- d) length and depth of unacceptable defects
- e) location and orientation of unacceptable defects
- f) name of operator
- g) date tested
- h) welders number
- i) drawing number
- j) repairs if any
4.14 Upon successful completion and acceptance of the ultrasonic inspection, the QC inspector shall complete all necessary QC inspection & record forms
The item shall be identified & recorded as inspected and accepted.
4.15 In the event that the ultrasonic inspection is unacceptable, the item shall be rejected and identified as such. The QC inspector shall record the results of the rejection on the relevant QC ultrasonic inspection form and amend all other QC records to reflect this rejection.
4.16 The rejected item shall be re-worked as required until it conforms to the required specification / tolerances, at which time it shall be re-inspected.
- Acceptance standers
5.1 AWS D1.1 & ASME B31.8
All indication that produce a response greater than 20 percent of the reference level shall , to the degree possible , be investigate to determine the location , shape , extent, and type of reflectors and shall be evaluated according to the following criteria:
5.1.1 Linear indications interpreted to be shallow crater cracks or star cracks, located at the weld surface, with a length less than 5/32 inch (3.96 mm) are acceptable. All other cracks are unacceptable, regardless of size or location in the weld.
5.1.2 Linear indications (other than cracks) interpreted to be open to the surface are unacceptable if they exceed 1 inch (25.4 mm) in total length in total length in a continuous 12 inch(304.8 mm) length of weld or 8 percent of the weld length.
5.1.3 Linear indications interpreted to be buried within the weld are unacceptable if they exceed 2 inch(50.8 mm) in total length in a continuous 12 inch length of weld of weld or 8 percent of the weld length.